In between coats 3 and 4, I used the knife to make the pattern for the sheath. I always make a pattern out of my favorite leather substitute.............. Cereal box paper board. This sheath will hold the knife by friction with a deep pocket that goes part way up the handle. It is a one piece with a folded belt loop.
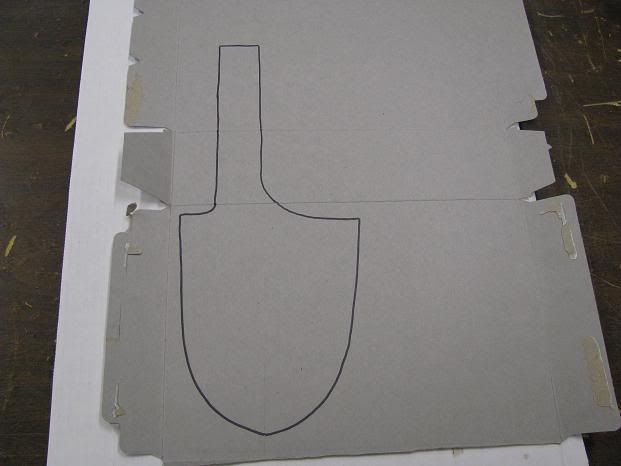
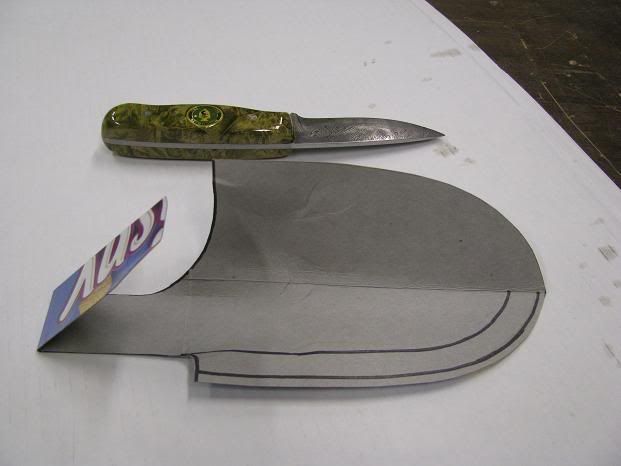
Seems like a good fit.
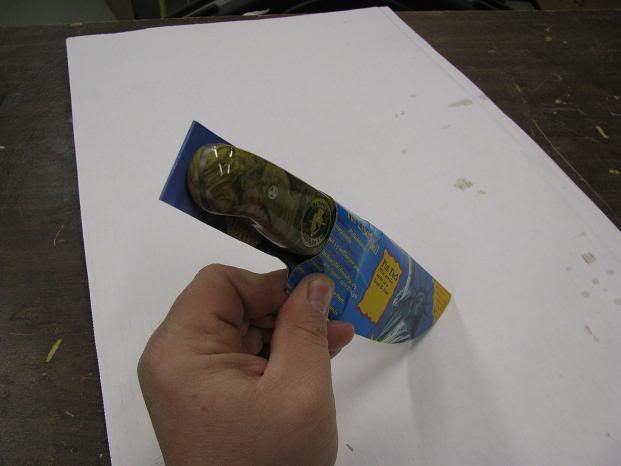
I then transfer the pattern to some creamy 8 Oz. Veg. tanned leather and cut it out with a razor knife.
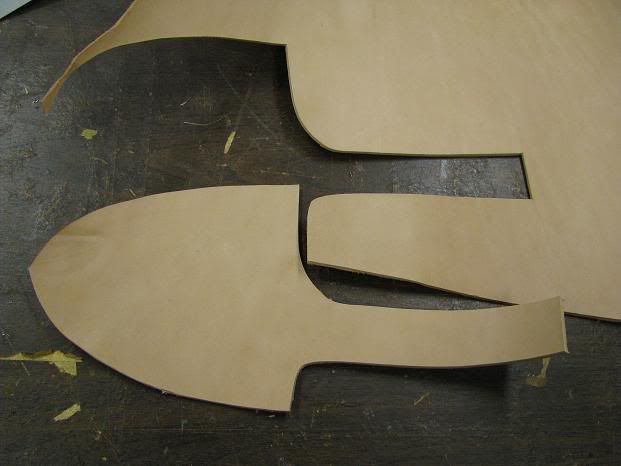
The first step is tapering the end of the belt loop so I have less bulk down in the pocket of the sheath.
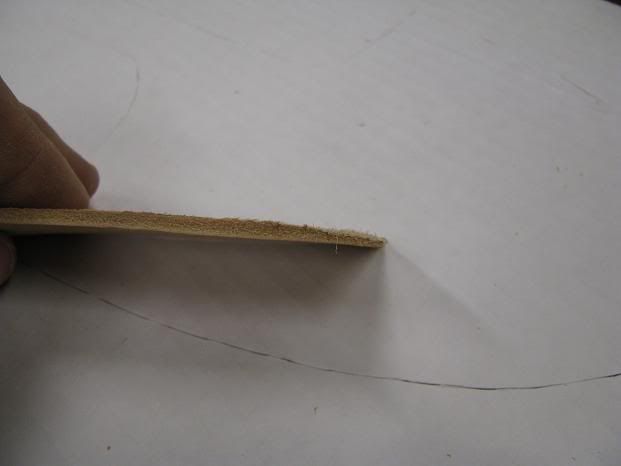
Then I crease and wet the leather to make the fold.
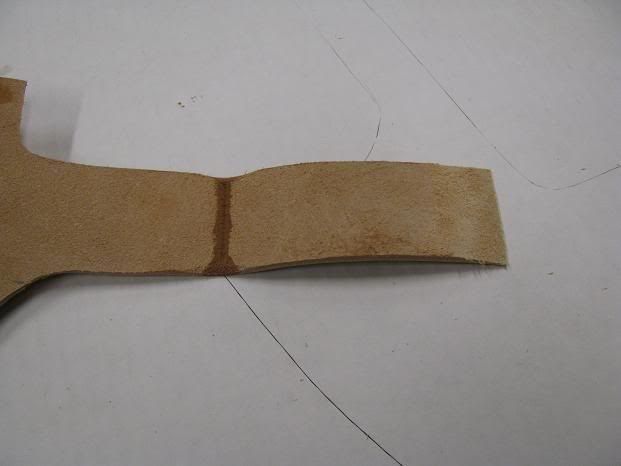
I hold everything in place for stitching with rubber cement.
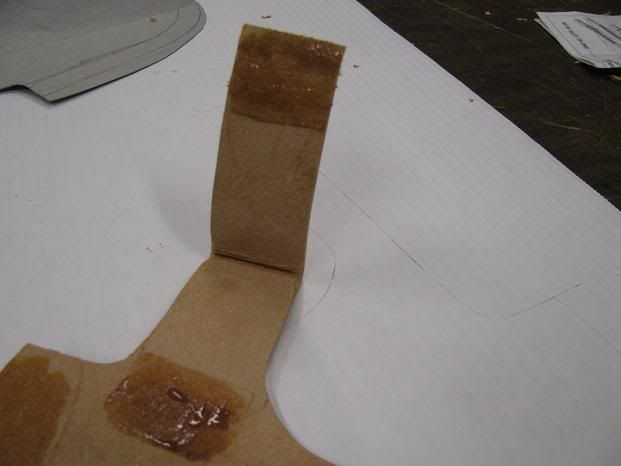
Then punch the stitching holes with a forked punch.
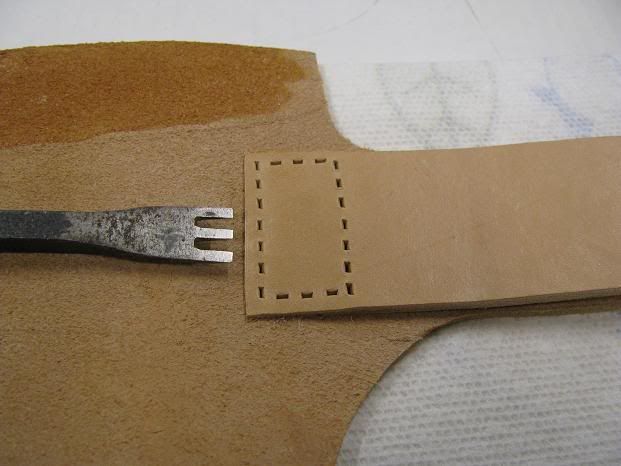
I want to see the stitching so I am using a waxed white cord. I put a needle at each end of the cord and stitch back and forth around the hole pattern.
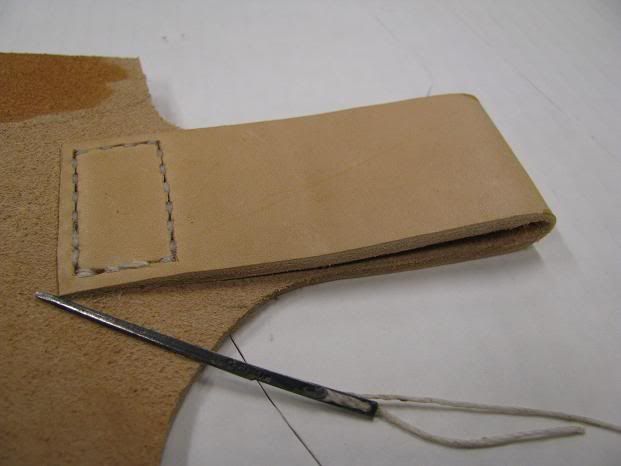
Before I fold the sheath in half, I add a welt made from 4 Oz. leather. It protects the stitching and adds a layer of leather thickness so the blade has room in the sheath.
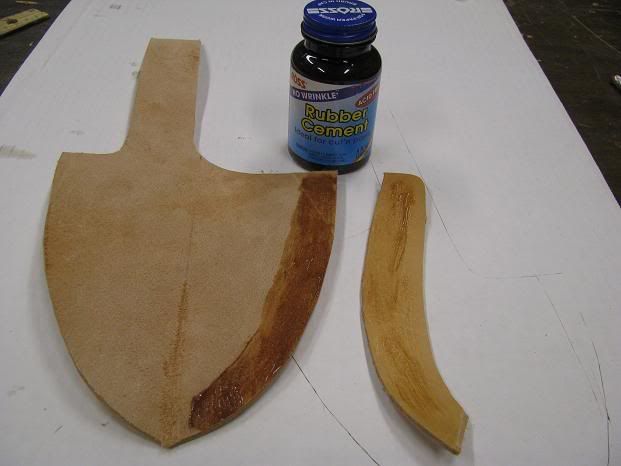
Once cemented, I wet the leather with a small paint brush and stamp in a pattern along the edge of where the stitching will go.
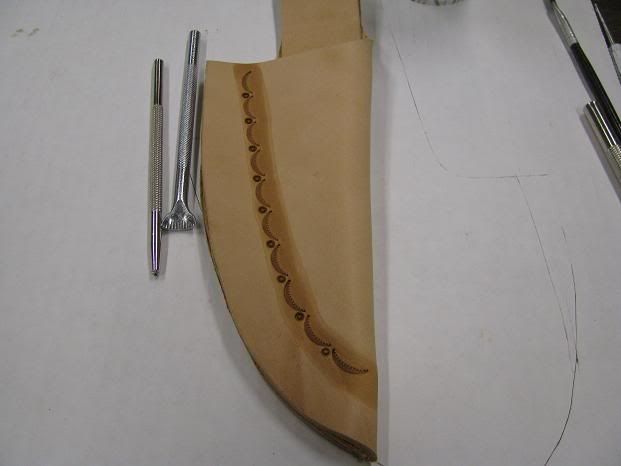
And then punch the stitching holes.
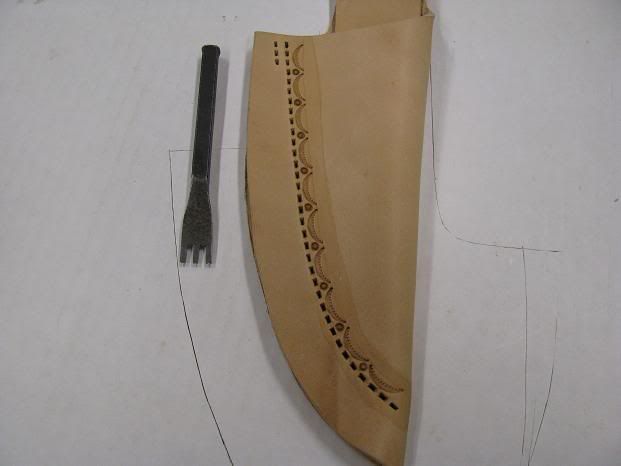
Using the same white cord and double needle method, I join the two sides and the welt.
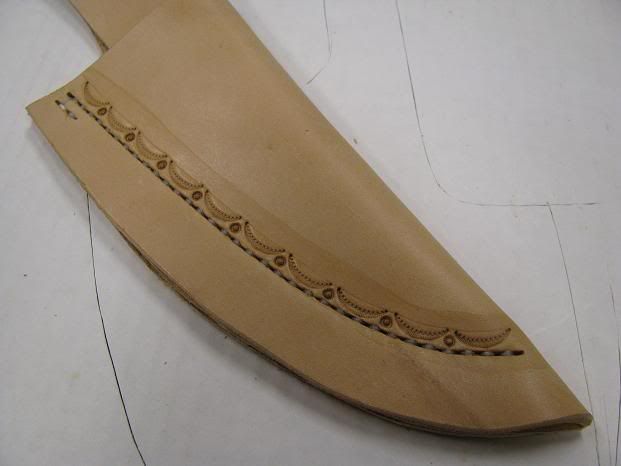
It's hard on the hands and a pliers is needed to pull the needle through but the end result looks pretty good.
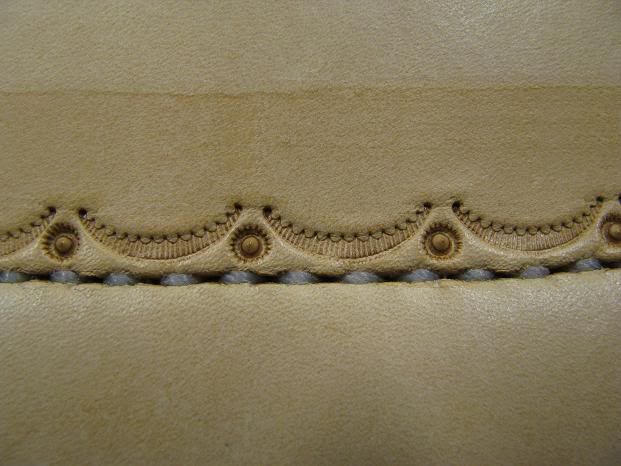
With the stitching complete, I trim off the excess leather.
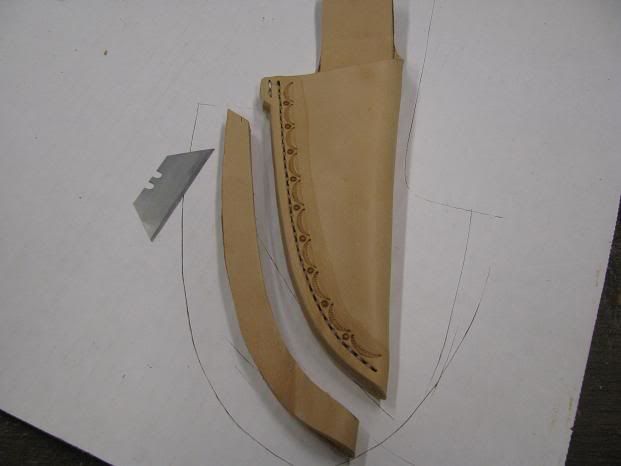
8 Oz. leather is pretty stiff but once wetted, It can be formed and molded like clay to the shape of the knife.
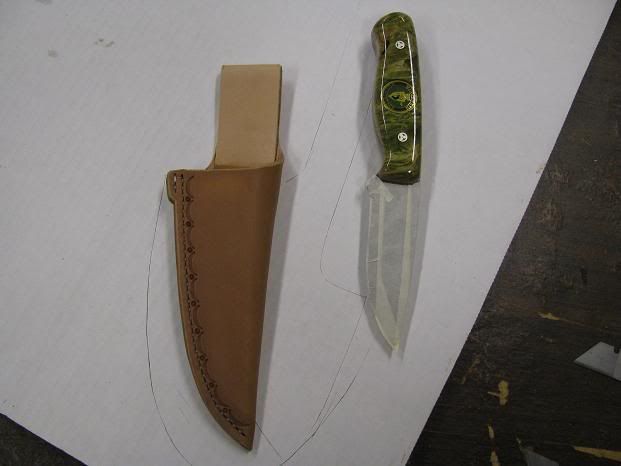
A little time at the end of a blow dryer, locks the shape into the leather.
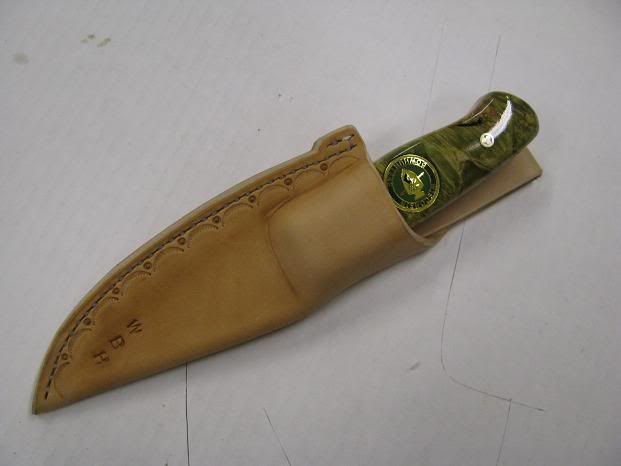
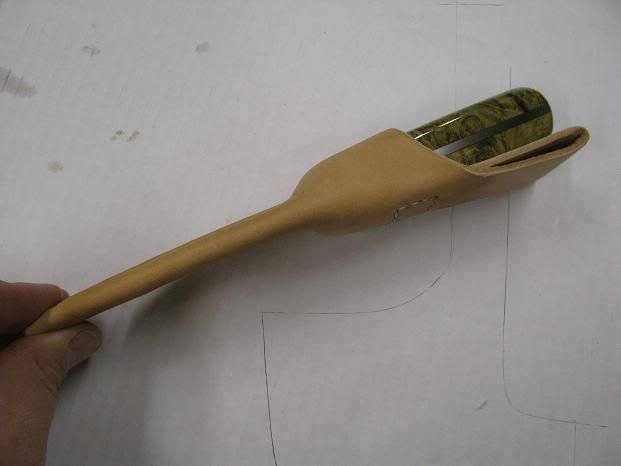
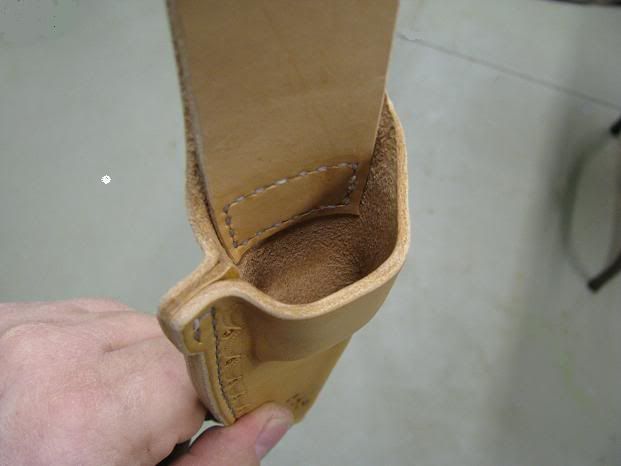
The next step is to give it a bit of color. I mixed, brown and Ox Blood and a little alcohol to get the reddish brown I was looking for.
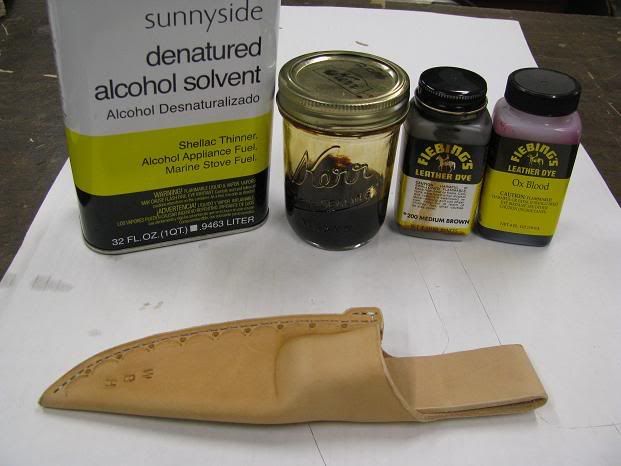
Once all the alcohol is evaporated, I need to replace all the oils lost during the forming and dyeing process. I use warm neatsfoot oil and a cotton daubber. The oil also darkens the leather a bit more.
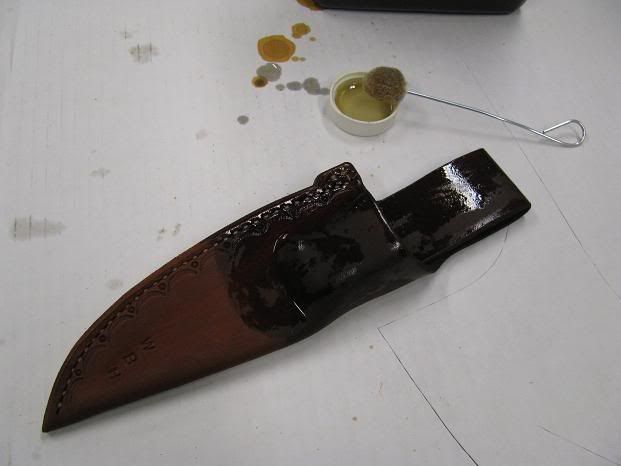
After sitting for a few hours wrapped in a paper towel, I warm the sheath with a blow dryer and apply a rub down of mink oil to further condition and water proof the leather. It turned out pretty good considering it's humble beginnings and will hopefully protect the knife better than it protected the cow that once wore it.
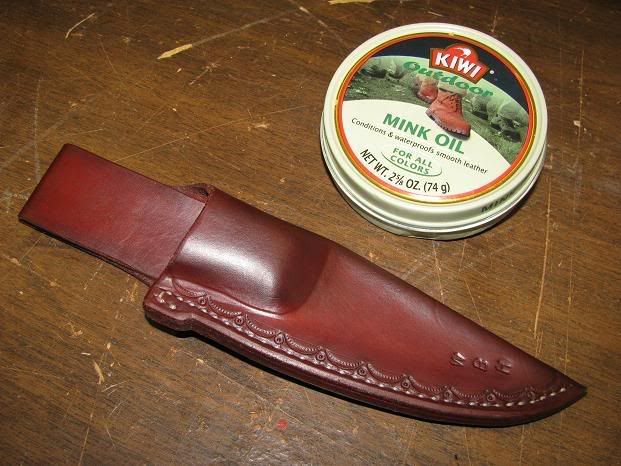
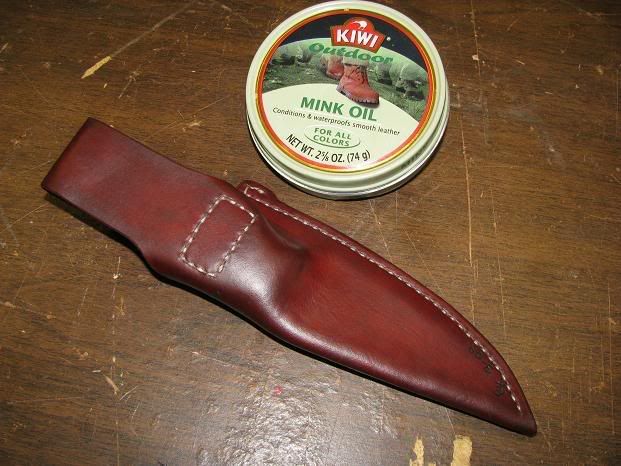
On the off chance that the future owner of this knife does not want to take her into the field and put her to work, I will design and build a display stand so it can sit all pretty like. The Damascus blade should not be stored in the sheath for long periods of time not to mention what a shame it would be to hide that blade from view.